Are you looking for an answer to the topic “Do gauge blocks need to be calibrated?“? We answer all your questions at the website Musicbykatie.com in category: Digital Marketing Blogs You Need To Bookmark. You will find the answer right below.
Like most test, measurement and inspection equipment, gage blocks require regular calibration to maintain accuracy. Scratches, gashes and other damage caused by wear and corrosion can negatively affect the blocks’ accuracy. Subjecting the gage blocks to calibration is the best way to verify accuracy.2) HOW OFTEN SHOULD GAGE BLOCKS BE CALIBRATED? Industry consensus is that gage blocks be calibrated every 1 to 3 years. Calibration intervals may be shortened or lengthened as needed.If the size of the gauge requires a stack of five blocks to make up the nominal size of the gauge the accuracy of each block must be known to 0.5/5 or 0.1 µm.
- Clean the gauge block using a chamois or soft cloth. …
- Measure the gauge block using a calibrated caliper. …
- Measure the gauge block at different locations using the calipers. …
- Record the date of calibration, and determine the next date to calibrate the blocks.
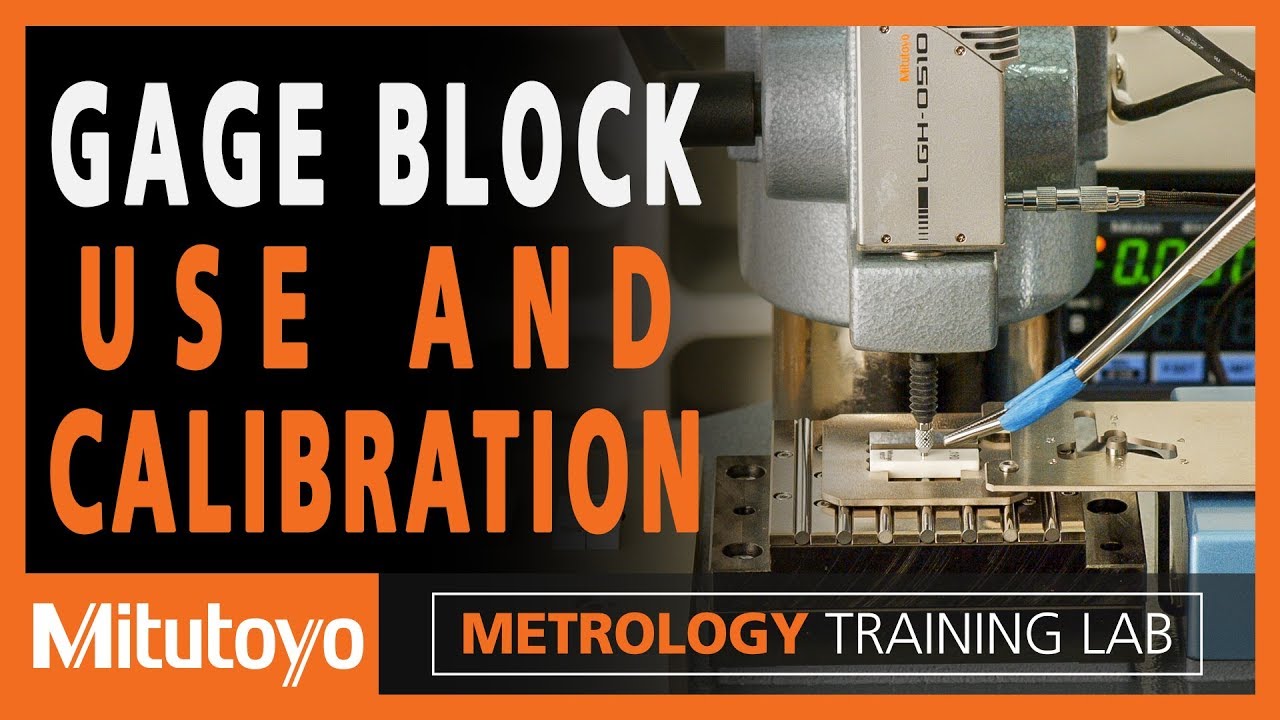
Table of Contents
How often should gauge blocks be calibrated?
2) HOW OFTEN SHOULD GAGE BLOCKS BE CALIBRATED? Industry consensus is that gage blocks be calibrated every 1 to 3 years. Calibration intervals may be shortened or lengthened as needed.
How do you calibrate gauge blocks?
- Clean the gauge block using a chamois or soft cloth. …
- Measure the gauge block using a calibrated caliper. …
- Measure the gauge block at different locations using the calipers. …
- Record the date of calibration, and determine the next date to calibrate the blocks.
Gage Block Introduction – How To Use and Calibrate Gauge Blocks
Images related to the topicGage Block Introduction – How To Use and Calibrate Gauge Blocks
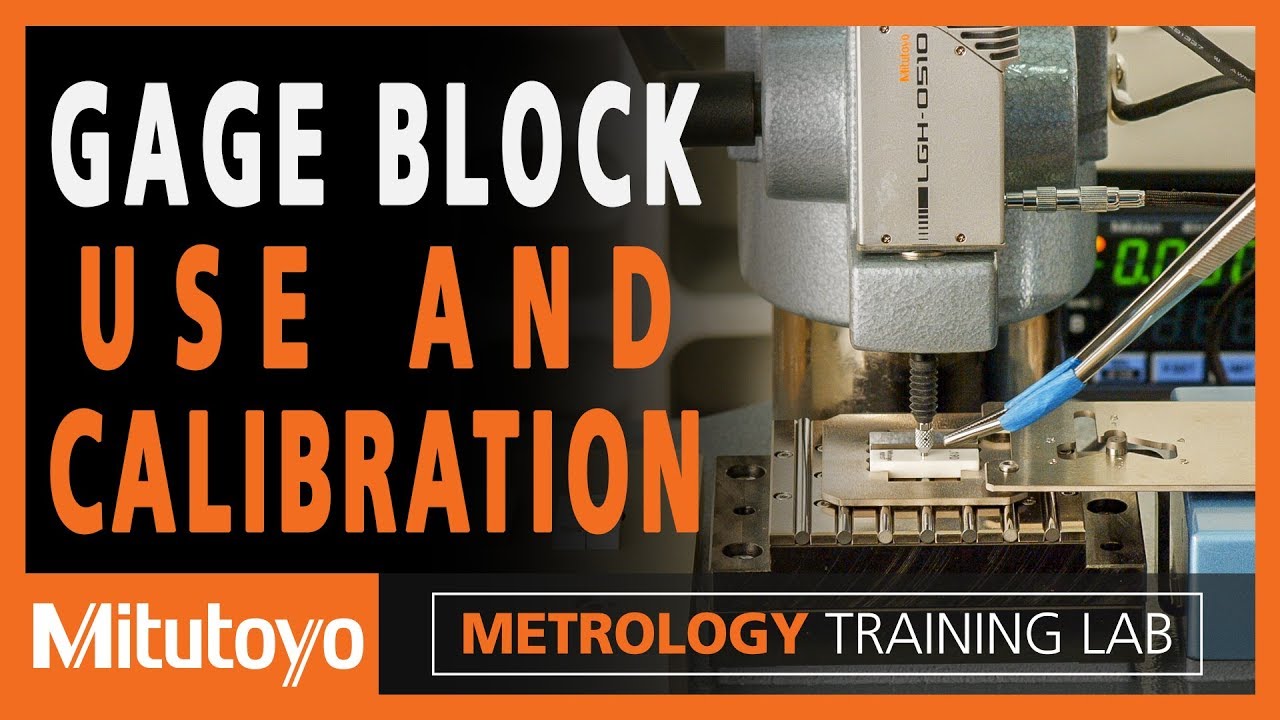
How accurate are gauge blocks?
If the size of the gauge requires a stack of five blocks to make up the nominal size of the gauge the accuracy of each block must be known to 0.5/5 or 0.1 µm.
How do you take care of gauge blocks?
Regularly cleaning gauge blocks removes excess debris and oils that can potentially damage the block’s surface. We suggest using a soft lint-free cloth and a few drops of Isopropanol before and after use. If you are using steel gauge blocks, wipe each gauge with a rust preventative oil after cleaning.
Why do gauge blocks wring together?
The source of the forces holding gage blocks together are thought to come from: Air pressure from the surrounding environment as the air is squeezed out when the blocks are slid together. Surface tension from oil that remains on the gage blocks or water vapor from the air that acts as an adhesive to hold them together.
Do radius gauges need to be calibrated?
The radius gages is considered an in an inherently stable device and will not require recalibration unless a special request is made by the user.
What is the best grade of gauge blocks?
Grade 0, Webber A1: The most popular grade of blocks: 1) it is accurate enough to perform 95% or more of all applications. This grade is recommended for general use. 2) most steel blocks are Grade 0, and steel is the most popular choice of gage block materials.
See some more details on the topic Do gauge blocks need to be calibrated? here:
Gauge Block Calibration: Things You Need to Know
Ideally, gauge block calibration should be performed once in 1 to 3 years according to Starrett. Again, it depends on your need. Methods of Gauge Block …
use-care-of-precision-gage-blocks.pdf – Starrett
Industry consensus is that gage blocks be calibrated every 1 to 3 years. Calibration intervals may be shortened or lengthened as needed. The frequency of …
Gage Block Calibration Methods – CrossCo – Cross Company
The mechanical length of a gage block is the length determined by mechanical comparison of a block to another block of known interferometrically determined …
How to Calibrate Gauge Blocks – HomeSteady
Measure the gauge block using a calibrated caliper. Verify that the reading on the caliper matches the specified dimension on the gauge block.
How to Use Master Calibration Blocks aka Gage Blocks
Images related to the topicHow to Use Master Calibration Blocks aka Gage Blocks
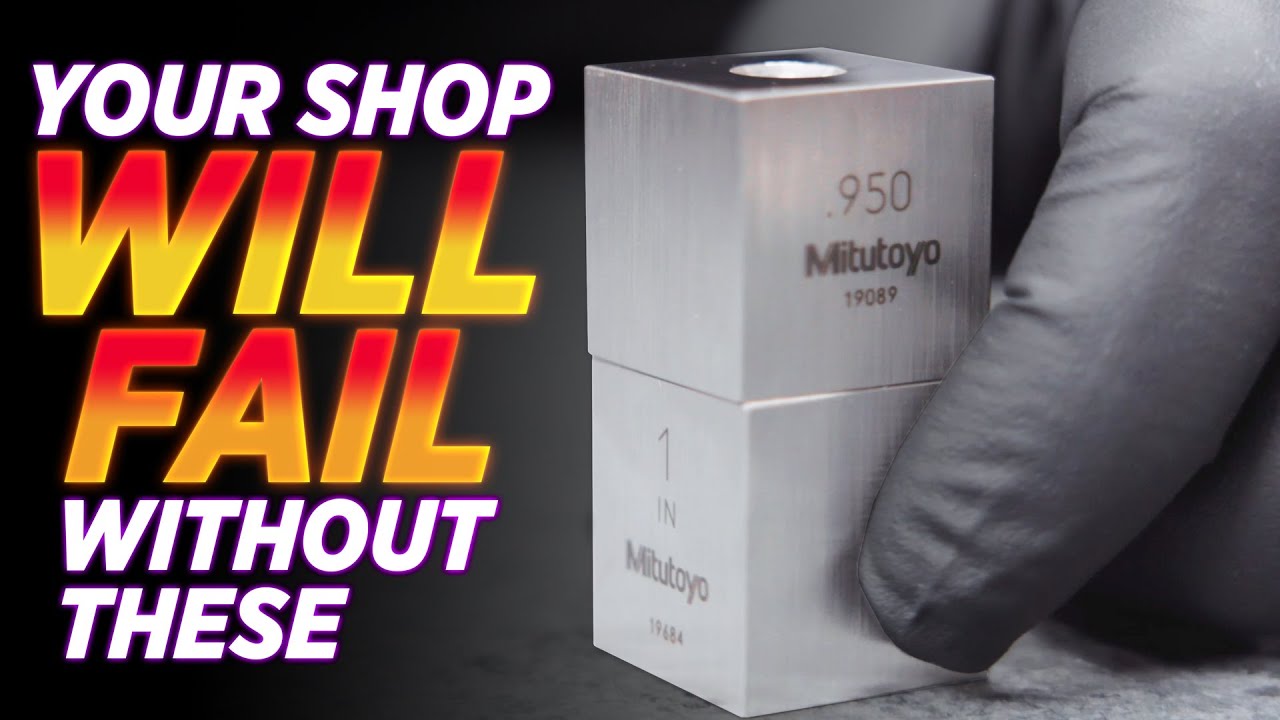
How accurately can gage blocks be wrung together?
Wringing is the process of sliding two blocks together so that their faces bond. Because of their ultraflat surfaces, when wrung, gauge blocks adhere to each other tightly. Properly wrung blocks may withstand a 300 N (67 lbf) pull.
Do vernier calipers need calibration?
What makes a Vernier caliper unique from other types of calipers is the inclusion of a vernier scale which enables these calipers to be even more precise. In order to ensure precision of measurements, it is important the calipers be maintained by calibrating them regularly and carefully.
Is standard for caliper checker?
The reference standard for testing the inside measurement is typically a caliper checker, a ring gage, or gage blocks and accessories. The default size for testing is between 0.75 in (20 mm) and 2 in (50 mm). For depth and step measurements, the reference standard is typically a gage block on a surface plate.
Why are different grades of gauge blocks used?
Gage (gauge) blocks are available in various grades, depending on their intended use. The grading criterion is tightness of tolerance on their sizes; thus higher grades are made to tighter tolerances and have higher accuracy and precision.
Which of the following is used to clean the gauge block before and after use?
Before use, clean gage blocks with mineral spirits, which leaves a very slight oily film for corrosion protection while the blocks are in use. Cleaning with alcohol is acceptable, but may leave the blocks so clean that they may be susceptible to corrosion.
How can you tell that you have wrung blocks together properly?
Slide the upper block back into full engagement under light pressure, at which point they should be wrung together ready for use. Worn or dirty blocks will not wring. The lapped surfaces of Precision Gage Blocks have a mirror finish, and they will adhere with surprising tenacity when wrung together.
Gage Block Calibration Process
Images related to the topicGage Block Calibration Process

Why ceramic slip gauges is better than steel slip gauges?
Why ceramic slip gauges is better than steel slip gauges? Explanation: Ceramic slip gauges are about 10 times more resistant to wear as compared to steel slip gauges. Natural stability and durability due to its low friction co-efficient make it more resistant.
Why are slip gauges called Johansson gauges?
Gauge blocks were invented in 1896 by Swedish machinist Carl Edvard Johansson. Hence the name “Johansson gauge blocks or “Jo-ey” or Jo gauge blocks for short.
Related searches to Do gauge blocks need to be calibrated?
- gauge blocks sticking together
- gauge block grade as 1
- gauge block grade chart
- acceptance criteria for pressure gauge calibration
- gauge block calibration procedure
- mitutoyo gage block tolerance chart
- gauge block tolerances
- types of gauge blocks
- do pressure gauges need to be calibrated
- how often should gauge blocks be calibrated
- what are gauge blocks used for
- do gauge blocks need to be calibrated
- how often do gauge blocks need to be calibrated
- how are gauge blocks calibrated
Information related to the topic Do gauge blocks need to be calibrated?
Here are the search results of the thread Do gauge blocks need to be calibrated? from Bing. You can read more if you want.
You have just come across an article on the topic Do gauge blocks need to be calibrated?. If you found this article useful, please share it. Thank you very much.